煤化工用鍋爐給水泵的故障分析及處理
2020-11-30何立根
(中天合創(chuàng)能源有限責(zé)任化工分公司,內(nèi)蒙古鄂爾多斯 017399)
鍋爐給水泵輸送高溫流體,運(yùn)行容易出現(xiàn)故障。中天合創(chuàng)能源有限責(zé)任公司熱電裝置使用的給水泵出現(xiàn)超電流、汽蝕余量不達(dá)標(biāo)及振動過大等現(xiàn)象,根據(jù)現(xiàn)場實(shí)際工藝要求進(jìn)行整改,通過葉輪切割、更換誘導(dǎo)輪等一系列方法完成整改,故障得以排除,現(xiàn)場運(yùn)行平穩(wěn),性能參數(shù)達(dá)到設(shè)計(jì)使用要求。(中天合創(chuàng)能源有限責(zé)任化工分公司,內(nèi)蒙古鄂爾多斯 017399)
一、前言
中天合創(chuàng)公司的大型煤化工是國家“十二五”新型煤化工示范項(xiàng)目,其熱電裝置5×490t/h的鍋爐設(shè)置平臺100%容量配備4臺(5#、6#、7#、8#)鍋爐定速給水泵,臥式9級雙殼體式,配備三相異步電動機(jī),參數(shù)見表1。
表1 設(shè)備基本參數(shù)

二、給水泵故障
該給水泵為9級雙殼體離心泵,軸封采用機(jī)械密封,軸承潤滑采用外供強(qiáng)制潤滑;泵為中心線支撐,進(jìn)出口均垂直向上,泵定子部分由吸入段、中段、排出段和導(dǎo)葉等組成,轉(zhuǎn)子部分由誘導(dǎo)輪、葉輪、軸、機(jī)械密封、軸承和聯(lián)軸器組件等組成,泵通過聯(lián)軸器由電動機(jī)驅(qū)動,從電動機(jī)方向看為順時針方向旋轉(zhuǎn)。如圖1所示。
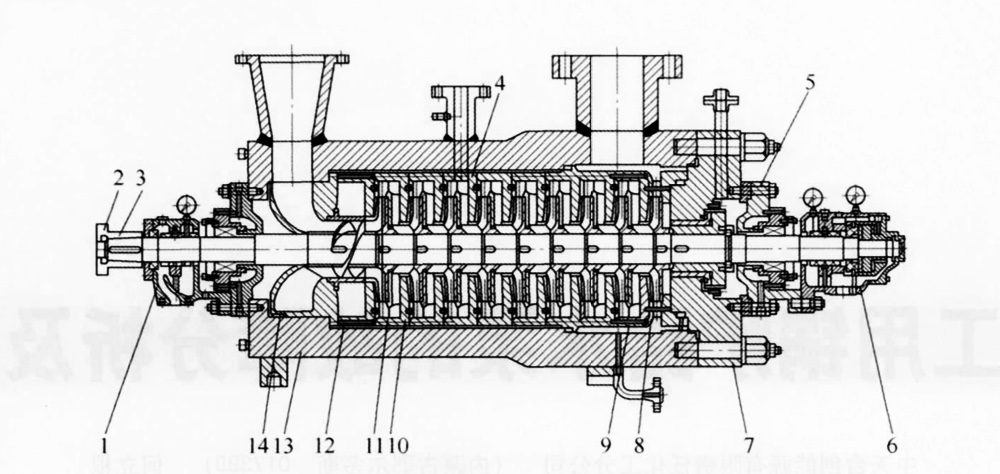
圖1 給水泵結(jié)構(gòu)
1.軸承部件;2.聯(lián)軸器部件;3.軸;4.抽頭中段;5.吐出冷卻室;6.推力軸承;7.泵蓋部件;8.末段導(dǎo)葉部件;9.末級中段;10.中段;11.導(dǎo)葉;12進(jìn)水段;13.筒體部件;14.吸入函體
4臺鍋爐定速給水泵參數(shù)相同,互換性高,7#泵開車后發(fā)現(xiàn)效率和汽蝕余量沒有達(dá)到用戶要求,其余3臺也出現(xiàn)了同樣的問題:1.軸承部件;2.聯(lián)軸器部件;3.軸;4.抽頭中段;5.吐出冷卻室;6.推力軸承;7.泵蓋部件;8.末段導(dǎo)葉部件;9.末級中段;10.中段;11.導(dǎo)葉;12進(jìn)水段;13.筒體部件;14.吸入函體
1)電動機(jī)超電流。
2)泵汽蝕余量過高。
3)在原速運(yùn)轉(zhuǎn)過程中振動偏大。
三、原因分析
針對出現(xiàn)超電流、汽蝕余量過高、振動偏大的故障進(jìn)行原因分析。
1.電動機(jī)超電流
現(xiàn)場測試流量達(dá)403m3/h(即額定流量590m3/h的68.31%)、揚(yáng)程1956m,電動機(jī)電流為264A(為額定值的100.4%),出現(xiàn)超電流現(xiàn)象。通過拆解分析,導(dǎo)致電動機(jī)超電流的主要原因如下。
1) 葉輪直徑設(shè)計(jì)偏大,揚(yáng)程偏離額定點(diǎn)太大,超10%,造成軸功率偏大,這是電動機(jī)超電流的原因之一。
2) 流體從泵進(jìn)口流入,經(jīng)葉輪、導(dǎo)葉,最后通過泵體流出的過程中,葉輪、導(dǎo)葉、泵體等鑄造精度不高,流動阻力增大,損失增大,效率偏低,也會使電動機(jī)超電流。
3) 經(jīng)兩次試驗(yàn)判斷筒體排出室面積偏小,有阻水現(xiàn)象,流體經(jīng)過排出室時不能光滑過渡,不符合逐漸把動能轉(zhuǎn)換為壓力能的趨勢。
2.汽蝕余量過高
從汽蝕試驗(yàn)數(shù)據(jù)來看泵汽蝕余量為12.66~13.66m,從泵的性能曲線來看汽蝕余量在13m左右,而協(xié)議要求的泵汽蝕余量為7m,嚴(yán)重超標(biāo)容易造成泵汽蝕,從而引起泵的振動甚至停泵。
影響泵汽蝕余量的因素主要有三個方面,誘導(dǎo)輪、裝置汽蝕余量和葉輪進(jìn)口幾何形狀。故障存在的原因之一是誘導(dǎo)輪的設(shè)計(jì)未達(dá)到工藝要求,原有的誘導(dǎo)輪外徑223mm,在流量649m3/h時,誘導(dǎo)輪揚(yáng)程為4m,汽蝕余量高,誘導(dǎo)輪的設(shè)計(jì)不達(dá)標(biāo);首級葉輪進(jìn)口幾何形狀也是影響汽蝕余量過高的原因,檢查發(fā)現(xiàn)葉輪進(jìn)口面積偏小,增大進(jìn)口流速,泵的汽蝕余量偏高,汽蝕性能下降;裝置汽蝕余量也是影響泵汽蝕余量的主要因素;增加進(jìn)口壓力,增大裝置汽蝕余量,改善汽蝕性能。
3.振動偏大
泵在運(yùn)行過程中振動噪聲明顯,由于超電流致使泵不能在額定工況點(diǎn)下運(yùn)行,流動不順暢,產(chǎn)生流體激振力,引起泵的振動噪聲;轉(zhuǎn)子轉(zhuǎn)動時不平衡,也會引起振動;泵的汽蝕余量偏大,容易發(fā)生汽蝕,伴隨著強(qiáng)烈的水擊而產(chǎn)生振動和噪聲;工裝坐架固定泵不牢固,電動機(jī)與泵高偏差過大,舉架過高,也是造成泵在運(yùn)轉(zhuǎn)過程中振動偏高的原因。
四、處理對策
針對電動機(jī)超電流、汽蝕不達(dá)標(biāo)和振動偏高等問題,進(jìn)行更換誘導(dǎo)輪、葉輪切割等一系列整改。
1.電動機(jī)超電流的故障處理
(1)次級葉輪切割 原4臺泵在裝置現(xiàn)場均出現(xiàn)超電流現(xiàn)象,其原因是揚(yáng)程偏高,軸功率偏大。首先對7#泵次級葉輪進(jìn)行計(jì)算切割量,根據(jù)GB3216—2005《回轉(zhuǎn)動力泵水力性能試驗(yàn)》標(biāo)準(zhǔn)的規(guī)定,當(dāng)葉輪平均出口直徑的切削量不超過5%時可以應(yīng)用切割相似換算定律進(jìn)行切割,設(shè)計(jì)點(diǎn)流量649m3/h時,揚(yáng)程為1933m,根據(jù)離心泵葉輪切割定律計(jì)算得出D=386mm,即水泵的葉輪由400mm切割至386mm,切割量為3.5%,小于5%,切割量符合國家GB3216標(biāo)準(zhǔn)中的要求,見表2。
表2 容差系數(shù)數(shù)值

對每臺泵的8個次級葉輪進(jìn)行切割,5#,6#由400mm切割到390mm;根據(jù)現(xiàn)場運(yùn)行報告7#、8#泵的流量與協(xié)議流量有13~16m3/h的差異,7#、8#由400mm切割到386mm。首級葉輪不切割。
(2)筒體排出室切削 筒體排出室的面積偏小。經(jīng)計(jì)算得出給水泵末級導(dǎo)葉斷面面積10×30mm×37mm=11100mm2,是出口面積的0.6倍。未切削前筒體斷面面積為312mm×25mm=8025mm2,是出口面積的0.5倍,不符合流道漸變趨勢,阻礙流動。切削后筒體面積為16050mm2,是出口面積的0.75倍,符合流道漸變趨勢。經(jīng)計(jì)算筒體內(nèi)徑由645mm加工到695mm,進(jìn)行出口內(nèi)孔邊緣打磨圓滑過渡,并進(jìn)行水壓試驗(yàn),泵體強(qiáng)度完全滿足現(xiàn)場實(shí)際運(yùn)行要求。
(3)局部處理為了流體順暢流動,對過流部件進(jìn)行局部處理,對首級葉輪葉片進(jìn)口邊進(jìn)行修尖處理,修正后葉片厚度2mm;對葉輪、導(dǎo)葉流道進(jìn)行D級拋光處理。

圖2 高速動平衡試驗(yàn)
葉輪修整與軸組裝,重新做高速動平衡試驗(yàn)(見圖2),按工藝要求平衡量≤10g,實(shí)際測最約為4g,滿足工藝要求。2.汽蝕余量過高的故障處理
給水泵技術(shù)協(xié)議要求汽蝕余量為7m,廠家實(shí)測為13.5m,需進(jìn)行誘導(dǎo)輪更換和首級葉輪處理。
(1)更換誘導(dǎo)輪 經(jīng)重新設(shè)計(jì),誘導(dǎo)輪外徑由223mm增加到225mm,更改后的誘導(dǎo)輪在設(shè)計(jì)流量649m3/h時,揚(yáng)程為6~7m;增加給水泵首級葉輪人入口壓力2~3m,泵汽蝕余量在首級葉輪不變的情況下降低2~3m;即流量649m3/h時,汽蝕余量為9~10m。

圖3 誘導(dǎo)輪
檢驗(yàn)誘導(dǎo)輪外圓首級葉輪蓋盤入口內(nèi)徑粗車預(yù)留余量≥5mm、符合工藝要求。對誘導(dǎo)輪進(jìn)行調(diào)質(zhì)處理、淬火加回火;HBW值檢驗(yàn),標(biāo)準(zhǔn)值180~250HBW,實(shí)測值220HBW,符合制造廠熱處理工藝要求,如圖4所示。

圖4 首級葉輪精加工
(2)調(diào)整首級葉輪 如圖4所示,首級葉輪進(jìn)行調(diào)質(zhì)處理、淬火加回火;首級葉輪直徑不變,增大葉輪入口面積,入口直徑由223mm增至235mm。入口面積增大后,流道過流面積趨勢為進(jìn)口部分凸起的曲線,符合汽蝕設(shè)計(jì)要求,加大入口直徑后的汽蝕余量比更換誘導(dǎo)輪后減低3-4m,即流量649m3/h時,汽蝕余量為5~6m。3.振動偏大的故障處理
根據(jù)GB29531—2013泵的振動測量與評價方法,該泵屬于第III類泵,試驗(yàn)測出的振動烈度為7.1mm/s,振動級別在c級,振動符合國家標(biāo)準(zhǔn)。
為了減少泵的振動和噪聲,提高運(yùn)行的安全性和穩(wěn)定性,對泵進(jìn)行以下處理。
1) 通過修正后的轉(zhuǎn)子部件動平衡試驗(yàn)可以有效降低泵的振動。
2) 汽蝕性能的提高有效降低泵的振動和噪聲。
3) 用固定坐架安裝固定給水泵;調(diào)整電動機(jī)與泵中心高的偏差。
按照“做一次低負(fù)荷性能試驗(yàn)—>一次拆卸解體—>逐級拆卸葉片—>回裝(一次裝配)—>做2500kW全速試驗(yàn)—>依據(jù)兩次試驗(yàn)結(jié)果分析確定故障原因—>排除故障—>二次拆卸解—>葉片切削加工—>轉(zhuǎn)子部件動/靜平衡試驗(yàn)—>葉片逐級回裝(二次裝配)—>整機(jī)性能試驗(yàn)—>出廠”的方法步驟進(jìn)行整改,如圖5所示,整改后進(jìn)行試驗(yàn)。

4臺泵整改后進(jìn)行試驗(yàn),依據(jù)GB3216—2005泵的性能應(yīng)在2980r/min下進(jìn)行;試驗(yàn)介質(zhì)為常溫清水(按GB3216—2005規(guī)定),泵機(jī)械密封沖洗水為自來水或工業(yè)水,開式試驗(yàn)臺;進(jìn)行運(yùn)轉(zhuǎn)試驗(yàn)、性能試驗(yàn)、振動測量和噪聲測量,試驗(yàn)結(jié)果滿足表1性能參數(shù)要求和現(xiàn)場使用要求。
五、結(jié)語
針對4臺給水泵運(yùn)行中出現(xiàn)的問題進(jìn)行整改并試驗(yàn),整改后的運(yùn)行參數(shù)符合用戶要求,振動和噪聲明顯減小,泵運(yùn)行平穩(wěn),符合國家標(biāo)準(zhǔn)和用戶使用要求。
1)通過切割葉輪和擴(kuò)大筒體內(nèi)徑,并進(jìn)行一系列的精密加工和試驗(yàn),整改后的揚(yáng)程、效率等參數(shù)達(dá)標(biāo),電動機(jī)不過載。
2)通過更換誘導(dǎo)輪和調(diào)整首級葉輪進(jìn)口尺寸,汽蝕余量達(dá)6m,現(xiàn)場運(yùn)行表明符合參數(shù)要求。
3)整改后進(jìn)行轉(zhuǎn)子部件動平衡試驗(yàn),現(xiàn)場安裝位置牢固到位,消除引起振動的因素。
參考文獻(xiàn)
【1】全國化工設(shè)備設(shè)計(jì)技術(shù)中心站機(jī)泵技術(shù)委會.工業(yè)泵選用手冊【M】.2版.北京:化學(xué)1:業(yè)出版社,2011.
【2】關(guān)醒凡.現(xiàn)代泵理論與設(shè)計(jì)【M】北京:中國宇航出版社,2011.
來源:《通用機(jī)械》2018年第9期